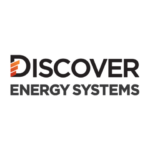
The Charged by Delta-Q program provides us with the opportunity to formalize what we have been doing and now promote it to a broader audience of potential partners and OEMs around the globe.
We work collaboratively with our clients from design conception to end-of-product life so we can tailor each project to their needs. Our manufacturing process reflects the unique nature of each project scope.
We control the process with dedicated Delta-Q production lines at all of our co-manufacturers, allowing us to introduce innovation opportunities. Our team keeps pace with global best practices while maintaining the high-quality standards our customers expect.
We have a global footprint through our network of manufacturing partners in Asia. Partnering with high-volume capacity manufacturers allows us to offer scalability and reliability to clients and projects at all levels.
Our largest contract manufacturing partner Flex, is a leading contract manufacturer with global distribution reach in the automotive, electrification, and healthcare industries.
By working closely with our engineers and manufacturing partners, we focus on a collaborative process with global best practices — from the design level to the final output.
Dedicated engineering and operations teams look critically at all products and processes, and always look for improvement opportunities.
From the “first handshake” to post-delivery of the product, we provide updated timelines and thorough communication directly to our customers.
Our manufacturing philosophy prioritizes value-added activities, keeping our processes LEAN and enabling us to pass along efficiencies and cost savings to our customers.
We follow a three-pronged approach to our quality process: at the supplier, assembly and customer levels.
Delta-Q’s chargers undergo rigorous automotive-grade testing validation methods such as vibration, shock, and thermal cycling to maximize product life.
Our advanced design for manufacturing methods creates products that minimize defects at the manufacturing stage.
Our products comply with North American and European safety and EMC standards (FCC-B and UNECE R10) and touch-safe voltage regulations, allowing easy integration into electric vehicles, and our manufacturing partners’ facilities are IATF 16949 and ISO 14001 certified. Our headquarters are ISO 9001 certified.
Read more about innovations and advances in our manufacturing process and facilities.
June 23 marks International Women in Engineering Day, a global celebration of…
Read MoreVancouver, BC – June 9, 2025 – Delta-Q Technologies (Delta-Q), a leading…
Read MoreFrom construction equipment to mobile elevated work platforms (MEWP), the electrification of…
Read MoreFrom an extensive network of vetted 3PL companies worldwide to consolidation at distribution centers, our logistics team meets customers where it makes sense.
As part of ZAPI Group, we tap into a global manufacturing and procurement network to support our existing customers worldwide and invest in emerging markets.