On highways, construction sites and factory floors worldwide, electric vehicles (EVs) of all shapes and sizes are rapidly replacing their gas-powered predecessors.
The shift to electric power is due to several factors, including the cost efficiencies of running and maintaining EVs, the environmental benefits of electric power over fossil fuels, and the operational and performance advantages EVs can deliver.
The migration speed from vehicles powered by internal combustion engines (ICEs) to those featuring an electric powertrain is accelerating year-over-year. In 2020, the number of electric cars on the world’s roads topped 10 million. They accounted for 4.6% of all new car registrations globally, up from 2.6% in 2019.
The growth of the electric powertrain has also rapidly created an e-mobility market—smaller personal and light commercial vehicles used for everything from city commuting to parcel deliveries.
As e-mobility becomes an increasingly popular option, many manufacturers of smaller vehicles are exploring how to incorporate electric powertrains into their vehicles.
This blog series guides organizations seeking to understand the decision-making process behind designing a new e-mobility vehicle. One of the first decisions to be made is choosing the most appropriate specifications for the electric powertrain based on the vehicle’s power and performance requirements.
Fundamental differences between electric motors and ICEs
ICE-powered vehicles rely on fuel (e.g., gasoline or diesel) being ignited and combusted within the engine to produce the energy needed to turn their wheels. In contrast, EVs are propelled by electric motors, which convert electricity from a rechargeable battery to mechanical power.
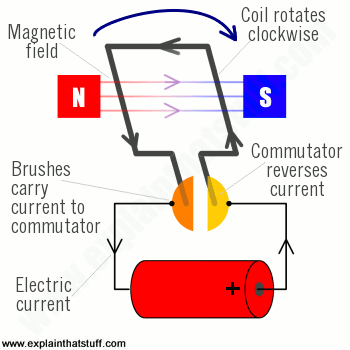
Source: https://www.explainthatstuff.com/electricmotors.html
Direct Current (DC) motors consist of an electromagnetic coil which sits inside a magnetic field. When a current is applied to the coil from the battery, electromotive forces cause it to start spinning within the magnetic field.
Let’s look at the main factors contributing to vehicle performance and how these differ between ICE-powered and battery-operated vehicles.
Torque
Torque is twisting or rotational force applied to an object moving around an axis. It is measured in pounds-feet (lb.-ft.) or Newton-meters (Nm).
This image illustrates 1 lb.-ft. of torque being applied to a wrench to twist a bolt:
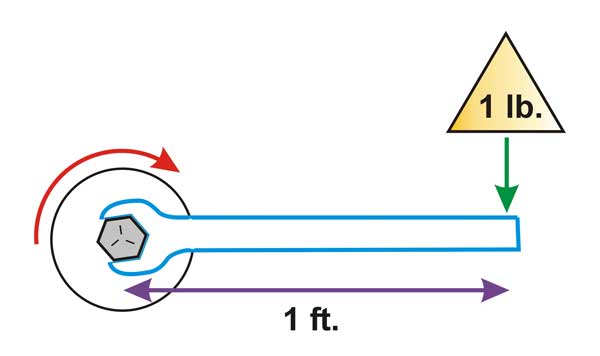
Source: https://delta-q.com/?p=5908&preview=true
In the context of a vehicle’s motor (both electric and ICE-powered), torque measures how much rotational force is available to turn the wheels when the engine exerts itself. The more torque an engine has, the better it will be at carrying out demanding tasks, such as towing or traveling up steep hills.
Electric motors generally have linear torque, meaning they can deliver peak torque instantaneously due to having fewer moving parts and low initial friction compared to ICEs. Because an ICE must contend with significant friction between its pistons and cylinders, it takes time to build up to its maximum torque.
Power and speed
A vehicle’s power output is measured in horsepower (HP) or kilowatts (kW) (one kilowatt is equal to roughly 1.34 horsepower).
An ICE must build up speed through acceleration until it reaches its maximum power and torque. This necessitates using a transmission system with several gears that optimize power output at different engine speeds.
A typical ICE torque/power curve looks something like this:
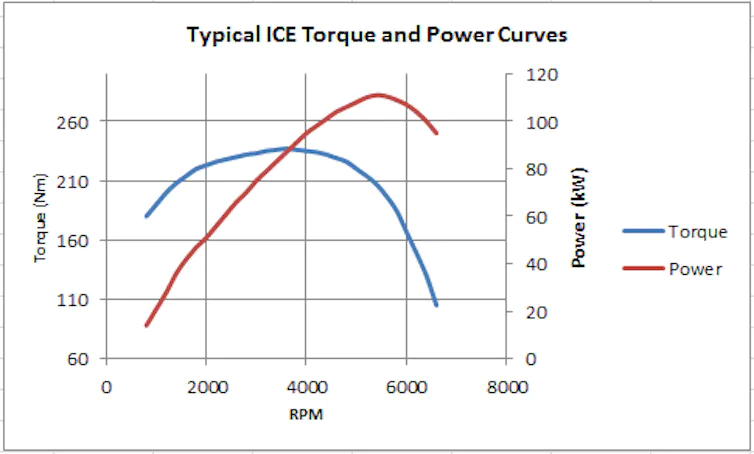
Source: https://theconversation.com/heres-why-electric-cars-have-plenty-of-grunt-oomph-and-torque-115356
In contrast, switching on an electric motor is similar to turning on a light bulb: its full power is available as soon as you flick a switch; no build-up time is needed. The peak power of an EV is always at zero RPMs.
A comparison of the ICE graph above with the electric motor graph below shows the electric motor is more efficient, delivering full torque from the start:
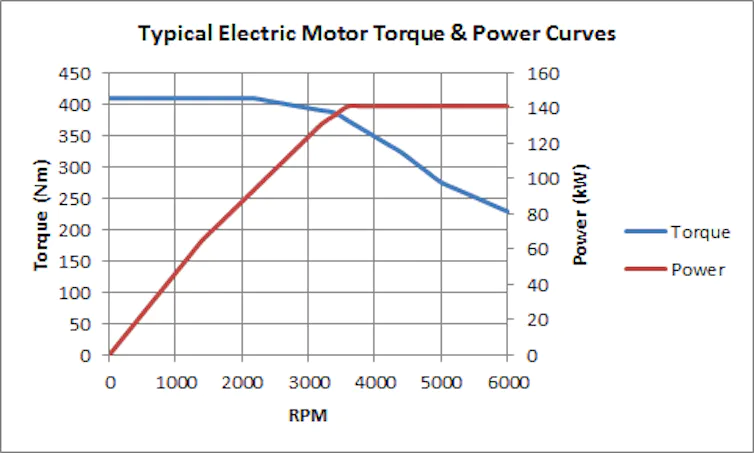
Source: https://theconversation.com/heres-why-electric-cars-have-plenty-of-grunt-oomph-and-torque-115356
There is a linear relationship between how fast the electric motor is spinning and the power required to spin it.
An electric motor’s power is directly proportional to the motor speed, measured in revolutions per minute (RPM) multiplied by the torque on the coil:
Power (HP)= [Torque (lb−ft) x Speed (rpm)] / 5250
Acceleration
An EV’s “instant torque” allows for incredible acceleration compared to a gas-powered vehicle, which enables Tesla’s Model S Plaid EV to reach 60mph in less than 2 seconds.
Top speed
While EVs have an advantage in acceleration over gas-powered vehicles, they have traditionally lagged in top speed. However, with EV technology evolving, this is no longer the case.
The top speed of an EV is limited to the maximum rotating speed of the motor. Dividing this by the gear ratio determines the rotational speed of the wheels, and multiplying that by the circumference of the tires gives the theoretical maximum speed of the vehicle:
Top Speed (mph)= (RPMGear / Ratio) x Tire Circumference x (1 hr / 60 mins)
Not only can electric motors enable much higher speeds than ICEs, and with greater efficiency (as seen in the graphs above), they can do so using only a single gear. This eliminates the need for a transmission system, which adds complexity and weight to ICE-powered vehicles.
Weight
Weight and how it impacts performance are significant factors to consider when designing any vehicle. In simple terms: as a vehicle gets heavier, it requires more energy to move.
Different powertrain choices can significantly affect the overall weight when comparing EVs and ICE-powered vehicles. The fuel weight in a gasoline-powered vehicle’s tank is likely to be much less than that of a battery required to drive a comparable EV.
With EV design, balancing battery weight against performance can create an interesting paradox. A heavier vehicle will take more power to move, but as more batteries are added to compensate for this, the total weight of the vehicle increases. Reducing vehicle size, choosing lighter materials, and limiting accessories will help reduce the power required to put the vehicle in motion.
Aerodynamics
The aerodynamic design of a vehicle is an important consideration because poor design can result in more energy being needed to accelerate and maintain speed.
A vehicle with poor aerodynamics will have greater drag, impeding acceleration, thus reducing its power efficiency. The faster a vehicle travels, the more drag it experiences (doubling an object’s speed quadruples its drag). Conversely, a vehicle with good aerodynamics will be less affected by drag.
Picking the right electric powertrain specifications
Understanding your vehicle’s performance requirements and other factors, such as weight, will enable you to choose the appropriate electric powertrain.
The primary decision to be made is deciding on an appropriate motor and controller that delivers the voltage and current required to meet your speed (voltage) and torque (current) requirements.
As with any development, you may face trade-offs between performance and cost. Generally, the higher the voltage, the more expensive the battery, so developing a high-performance EV will increase the cost.
Learn more
For more information on electric motors and the design aspects of e-mobility vehicles, speak with a motor/controller expert like InMotion Technologies. InMotion has been designing and manufacturing electric motors and power electronics for commercial vehicles since the 1960s. Part of the ZAPI Group, it is a global supplier of electric motors, motor control units and auxiliary electronic equipment for industrial and commercial vehicles.